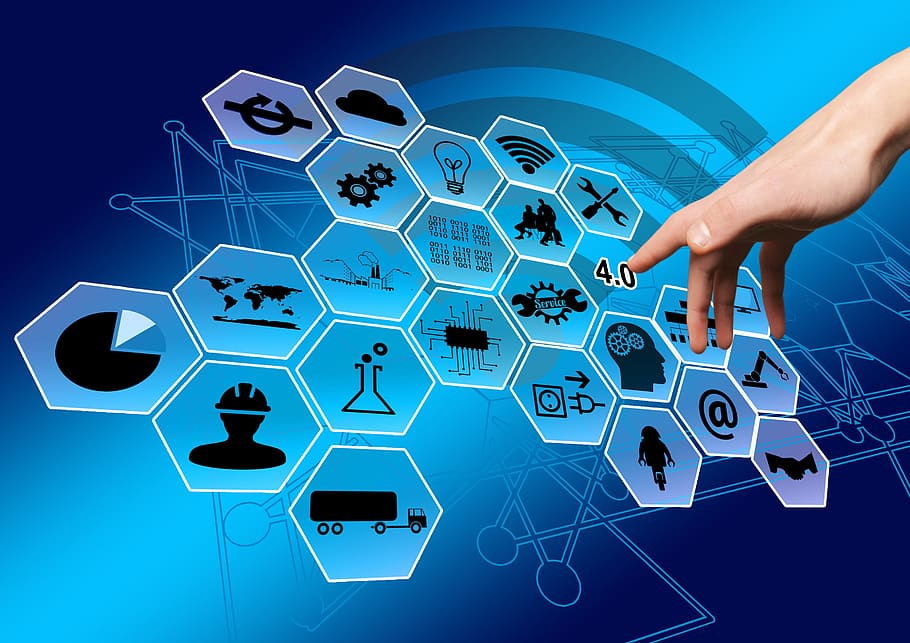
In the vast world of industrial manufacturing, where machines hum and factories buzz with activity, there exists a silent hero – sensors. These unassuming devices play a crucial role in keeping the wheels of industry turning smoothly. Let’s embark on a journey to unravel the mysteries of sensors, understanding how they work and why they are indispensable in the realm of industrial manufacturing.
“In the intricate dance of gears, sensors emerge as unsung heroes, ensuring precision in every product.”
Understanding Sensors
At its core, a sensor is like a super-sensitive detective for machines. It gathers information from the environment and reports back to the machines, helping them make informed decisions. Imagine it as the eyes and ears of the manufacturing process, tirelessly observing and listening.
Types of Sensors
- Temperature Sensors: Temperature sensors monitor how hot or cold things are. They ensure that machines operate within safe temperature ranges, preventing overheating.
- Pressure Sensors: Like a digital blood pressure monitor for machines, these sensors keep track of pressure levels. They are vital in maintaining optimal conditions for various manufacturing processes.
- Proximity Sensors: Acting as the ‘personal space’ detectors for machines, proximity sensors identify the presence or absence of an object nearby. This prevents collisions and ensures smooth operations.
- Motion Sensors: Ever wondered how robots ‘see’ obstacles? Motion sensors are the answer. They detect movement and help machines navigate their surroundings safely.
The Role of Sensors in Industrial Manufacturing
In the bustling world of industrial manufacturing, precision and efficiency are non-negotiable. Here’s how sensors contribute to achieving these goals.
Ensuring Product Quality
- Quality Control Sensors: These sensors are the guardians of quality. They meticulously inspect products, identifying any defects and ensuring that only top-notch items leave the production line.
- Vision Sensors: Just like human eyes, vision sensors capture images to verify product details. They play a vital role in maintaining the integrity of the manufacturing process.
Enhancing Safety
- Emergency Stop Sensors: In the event of a potential hazard, these sensors act as the emergency brakes for machines. They swiftly bring operations to a halt, preventing accidents.
- Smoke and Gas Sensors: Safety first! These sensors detect the presence of harmful gases or smoke, alerting the system to take necessary precautions.
Optimizing Efficiency
- Automated Guided Vehicles (AGVs): These futuristic machines navigate through factories autonomously, thanks to sensors. They transport materials efficiently, reducing the need for manual intervention.
- Energy-Efficiency Sensors: Industrial plants are energy-hungry, but sensors help optimize energy consumption. They ensure that machines operate only when needed, promoting sustainability.
Challenges Faced by Sensors
Just like any hero, sensors face challenges in their quest to keep industries running smoothly. Understanding these challenges is crucial to appreciating the complexities involved.
Environmental Factors
- Dust and Debris: In a factory environment, sensors encounter dust and debris. Regular maintenance is essential to ensure their accuracy and longevity.
- Extreme Temperatures: Whether it’s scorching heat or freezing cold, sensors brave it all. However, extreme temperatures can affect their performance, emphasizing the need for robust designs.
Compatibility Issues
- Integration Challenges: Not all sensors speak the same language. Ensuring seamless integration between different sensor types and machines requires careful planning and technical finesse.
- Upgradation Dilemmas: As technology evolves, older sensors may struggle to keep up. Upgrading systems while maintaining compatibility is a delicate balancing act.
Practical Application
Let’s imagine a car manufacturing plant where sensors are like vigilant guardians. As cars move along the assembly line, vision sensors inspect each part, ensuring they fit perfectly. If a flaw is detected, the quality control sensors halt the line, alerting workers to fix the issue. Proximity sensors ensure safe distances between vehicles, preventing collisions. In this way, sensors play a hands-on role in creating flawless cars, ensuring safety, and boosting efficiency.
Real-world Impact
Consider a scenario where a faulty sensor fails to detect a defective component in a smartphone assembly line. The defective phones reach customers, causing dissatisfaction and tarnishing the company’s reputation. On the other hand, well-functioning sensors prevent such mishaps, ensuring that only top-quality products reach the market. This not only safeguards the company’s image but also builds trust among consumers, showcasing the real-world impact of sensors in manufacturing.
“The real-world impact of well-functioning sensors goes beyond efficiency – it builds trust and safeguards reputations.”
Conclusion
In the intricate dance of gears and the rhythmic hum of machinery, sensors emerge as unsung heroes. Their ability to perceive, analyze, and communicate is the backbone of industrial manufacturing. From ensuring product quality to enhancing safety and optimizing efficiency, sensors play a pivotal role in shaping the future of industry.
In conclusion, the next time you marvel at a perfectly manufactured product, remember the silent workforce of sensors working tirelessly behind the scenes. They are the guardians of precision, the custodians of safety, and the architects of efficiency in the dynamic landscape of industrial manufacturing.