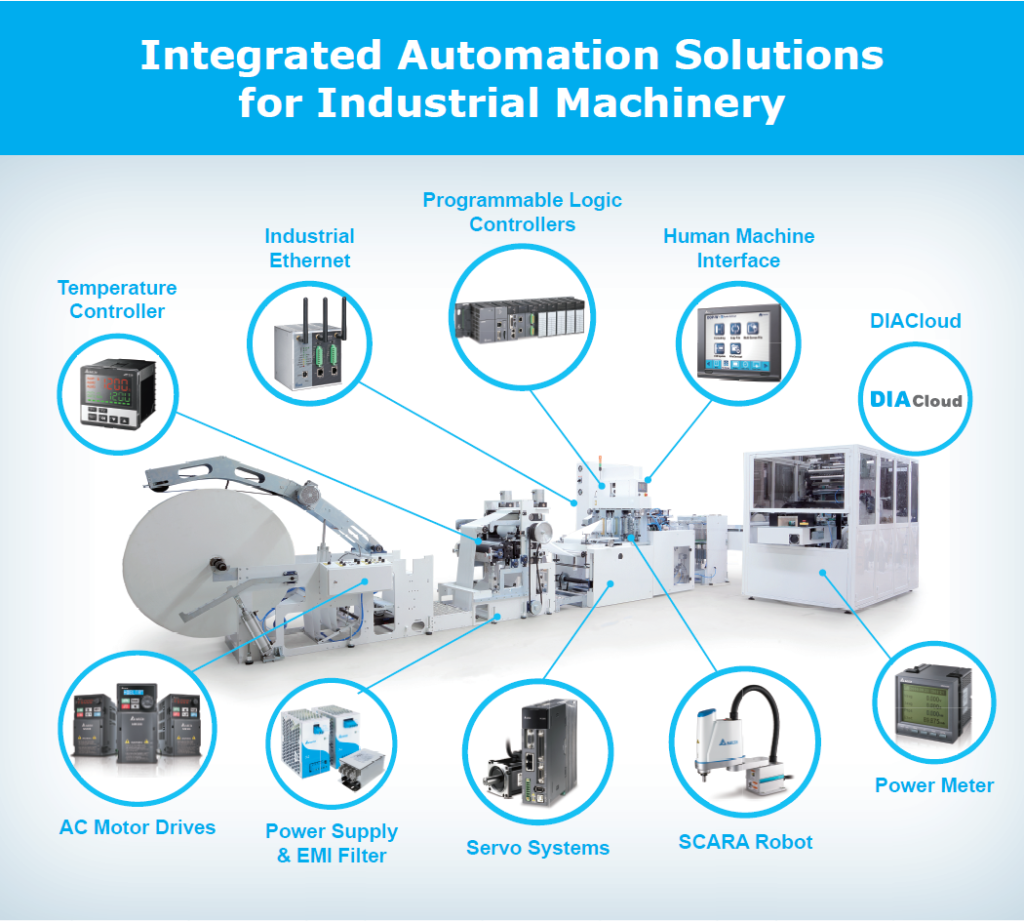
Industrial manufacturing, the powerhouse behind our everyday gadgets and machinery, relies on a fascinating duo known as Variable Frequency Drives (VFD) and Servo Drives. These motor drives are the unsung heroes working tirelessly behind the scenes, ensuring our factories hum with efficiency. Let’s take a closer look at these technological marvels and understand their role in the realm of Industrial Manufacturing.
“Efficiency Unleashed: Motor drives transform manufacturing, optimizing energy use and boosting productivity.”
The Basics of Motor Drives
At the heart of many manufacturing processes are electric motors, the workhorses responsible for transforming electrical energy into mechanical motion. Motor drives, like VFDs and Servos, act as the brains of these motors, regulating their speed, torque, and position. In simpler terms, they control how fast the motor spins and how much power it exerts.
Variable Frequency Drives (VFD)
Imagine a car with a pedal that controls both speed and power. VFDs work similarly for electric motors. They allow manufacturers to vary the frequency and voltage supplied to the motor, giving them precise control over its speed and torque. This not only enhances efficiency but also prolongs the motor’s life.
In practical terms, VFDs are like the conductors of an orchestra, dictating the tempo and intensity of the performance. In an industrial setting, this translates to energy savings, smoother operations, and the ability to adapt to different production needs.
Servo Drives
Now, let’s shift our focus to Servo Drives. If VFDs are conductors, Servos are the choreographers. They excel in precision control, ensuring the motor stops, starts, and moves with utmost accuracy. Servo Drives are crucial for applications where precise positioning is non-negotiable, such as robotic arms on assembly lines.
In a nutshell, Servo Drives make sure the industrial dance follows the choreography to the letter. They excel in tasks requiring finesse and accuracy, delivering the right moves at the right time.
Applications in Industrial Manufacturing
VFDs: Boosting Efficiency and Savings
In the bustling world of industrial manufacturing, efficiency is the name of the game. VFDs play a pivotal role by enabling the motor to operate at the optimum speed for a given task. Whether it’s a conveyor belt, a pump, or a fan, VFDs ensure the motor delivers just the right amount of power, preventing unnecessary energy consumption.
Moreover, VFDs offer a soft start and stop feature, reducing wear and tear on the motor. Think of it as a gradual acceleration and deceleration rather than a sudden jolt – a simple yet effective way to extend the lifespan of machinery.
Servos: Precision in Every Move
When it comes to applications demanding precision, Servo Drives take the spotlight. In robotics, CNC machines, and other automated systems, Servos ensure that every movement is accurate to the millimeter. Picture a robot delicately placing components on a circuit board – that’s the magic of Servo Drives at play.
The ability to precisely control position, speed, and torque makes Servos indispensable in tasks where human-like precision is required. In the realm of industrial manufacturing, this translates to higher quality products and streamlined processes.
Technological Advancements and Future Trends
As technology continues its relentless march forward, the landscape of motor drives in industrial manufacturing is evolving too. The integration of smart technologies and IoT (Internet of Things) is shaping the future of motor drives.
Smart VFDs
Smart Variable Frequency Drives go beyond basic speed and torque control. They communicate with other devices on the factory floor, exchanging information to optimize overall efficiency. These VFDs are like wise mentors, constantly learning and adapting to changing production demands.
IoT-Enabled Servos
Servo Drives equipped with IoT capabilities open up new possibilities for remote monitoring and predictive maintenance. Imagine receiving a notification on your phone before a Servo motor shows any signs of wear – that’s the proactive approach enabled by IoT integration.
Practical Application
Let’s imagine a factory that produces widgets using various machines. By implementing Variable Frequency Drives (VFDs) and Servo Drives in the production line, the factory can achieve significant energy savings and enhance overall efficiency.
For instance, when the demand for widgets is low, VFDs can reduce the speed of the machines, conserving energy. As demand increases, VFDs can ramp up the speed to meet production needs. On the other hand, Servo Drives can ensure precise movements in tasks such as packaging and assembly, minimizing errors and reducing waste.
In this practical example, the integration of motor drives not only optimizes energy usage but also allows the factory to adapt swiftly to varying production demands, ultimately improving the bottom line.
Real-world Impact
Consider a large-scale manufacturing plant that adopts VFDs and Servo Drives across its operations. The real-world impact is profound. The plant experiences a substantial reduction in energy costs due to the optimized usage facilitated by VFDs. Additionally, the precision and accuracy brought by Servo Drives lead to a significant decrease in defective products and material wastage.
“Precision Redefined: Servo Drives ensure every move counts, minimizing errors and maximizing quality.”
Conclusion: The Powerhouse Behind the Machines
In the grand symphony of industrial manufacturing, motor drives, specifically VFDs and Servos, play a crucial role. They are the silent architects of efficiency, the maestros of precision, and the guardians of longevity for our machines.
As we delve into the complexities of VFDs and Servos, it becomes evident that their significance extends far beyond the factory floor. These technologies not only drive motors but also drive progress, making industrial manufacturing smarter, more efficient, and ready for the challenges of tomorrow. So, the next time you marvel at the seamless operation of a production line, remember that behind the scenes, VFDs and Servos are orchestrating the performance, ensuring a harmonious dance of machinery in the world of industrial manufacturing.
The inputs and outputs of these drives vary based on the model and application. There are several manufacturers that produce them and offering a range of options for different needs and technical requirements (communication interfaces).
- Upgrading and Retrofit Industrial Machines
- Types of Automation Systems
- The Role of Industrial Automation
- The Future of Machine Automation
- Switchgear for Power Controls
- Switches: Types and Uses
- Streamlining Processes with Valve Automation
- Streamline Process with Automation
AC Drive: Variable Frequency Drive
Temperature Sensors
- Upgrading and Retrofit Industrial Machines
- Types of Automation Systems
- The Role of Industrial Automation
- The Future of Machine Automation
- Switchgear for Power Controls
- Switches: Types and Uses
- Streamlining Processes with Valve Automation
- Streamline Process with Automation