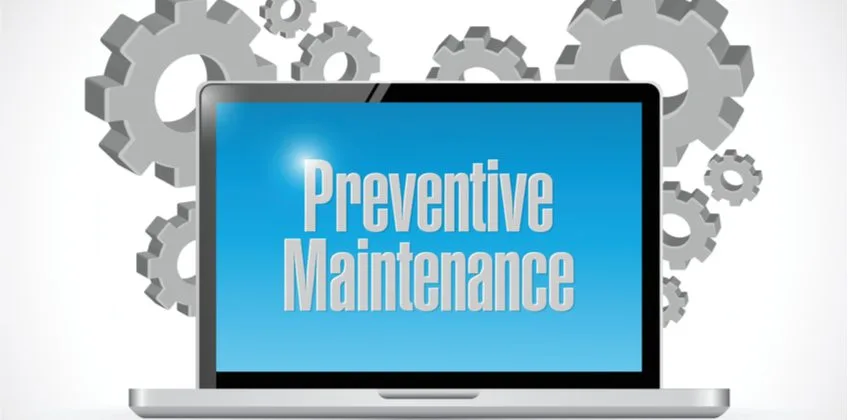
In the vast realm of Industrial Manufacturing, where machines hum and gears turn, the key to smooth operations lies in an often-overlooked hero – Preventive Maintenance. Let’s unravel the significance of this crucial practice for Preventive Maintenance and understand how it enhances productivity with performing Preventive Maintenance.
“Regular care keeps our machines humming, ensuring uninterrupted production.”
What is Preventive Maintenance?
Preventive Maintenance is like giving a gentle hug to your machines before they even think of getting tired. It’s a planned approach to keep equipment in good working condition by performing routine tasks. Instead of waiting for a machine to break down, we pamper it with regular care.
Why Pamper Machines?
Maintaining machines might seem like a lot of extra work, but it’s like brushing your teeth to avoid a toothache. Here’s why we pamper our machines:
- Avoiding Breakdowns: Preventive Maintenance helps us catch potential issues early, preventing sudden breakdowns. It’s like fixing a leaky faucet before it floods the kitchen.
- Longer Lifespan: Just like eating healthy and exercising keeps us going, regular care ensures a longer life for our machines.
- Cost Savings: Fixing a small issue is way cheaper than replacing a whole machine. Preventive Maintenance helps save money in the long run.
Components of Preventive Maintenance
Let’s break down Preventive Maintenance into its super basic components:
1. Routine Inspections
Imagine giving your car a quick check before a long journey. Routine inspections involve looking at the machines regularly to catch any signs of trouble. It’s like a health checkup for machines.
2. Lubrication
Machines have moving parts that need a bit of love. Lubrication is like giving them a massage – it reduces friction, ensuring everything runs smoothly.
3. Replacement of Wearable Parts
Just like changing the tires on a bicycle, machines need new parts too. We replace worn-out parts before they cause trouble, ensuring continuous smooth operation.
4. Calibration
Think of calibration as adjusting your watch to make sure it shows the right time. Machines have sensors and gauges that need to be accurate for optimal performance.
Importance in Industrial Manufacturing
Now, let’s dive into how Preventive Maintenance is a game-changer in the world of Industrial Manufacturing:
1. Uninterrupted Production
Imagine a factory humming with activity. Preventive Maintenance ensures this hum continues without sudden pauses. By addressing potential issues beforehand, it keeps the production line flowing smoothly.
2. Enhanced Safety
A safe workplace is a happy workplace. Regular maintenance not only prevents machine malfunctions but also ensures a safer environment for the workers. It’s like having a reliable friend watching your back.
3. Cost-Effective Operations
Shutting down production due to a breakdown can be expensive. Preventive Maintenance reduces the chances of unexpected failures, saving both time and money. It’s like investing a little to save a lot.
4. Improved Product Quality
Quality is the name of the game in Industrial Manufacturing. Maintained machines produce consistent and high-quality output. Preventive Maintenance is like having a quality control superhero on your team.
Implementing Preventive Maintenance – Super Easy Steps
Now that we understand the significance, let’s explore how to implement Preventive Maintenance in the simplest way possible:
1. Create a Schedule
Imagine having a to-do list for your machines. A schedule ensures that every machine gets the attention it deserves at the right time.
2. Train Your Team
Just like teaching a friend how to ride a bike, ensure your team knows how to perform basic maintenance tasks. This empowers them to contribute to the well-being of the machines.
3. Keep Records
Maintaining records is like keeping a diary for your machines. It helps track their health over time and allows for better planning.
4. Embrace Technology
Technology is our friend. Use sensors and monitoring systems to keep an eye on your machines. It’s like having a personal health tracker for each machine.
Practical Application
Imagine your car needing a regular check-up to avoid sudden breakdowns. That’s like Preventive Maintenance for machines in factories. By sticking to a schedule, inspecting regularly, and changing parts when needed, you keep the machines humming smoothly, just like your car stays on the road without unexpected stops.
Real-world Impact
In a real-world scenario, think about a factory that skips Preventive Maintenance. Suddenly, a crucial machine breaks down, causing production to halt. The impact? Delays in delivering products, upset customers, and extra costs for emergency repairs. Embracing Preventive Maintenance could have avoided this, ensuring a steady workflow and happy customers.
“Preventive Maintenance is like a health checkup for machines, saving both time and money.”
Conclusion
In the grand orchestra of Industrial Manufacturing, Preventive Maintenance plays the role of the conductor, ensuring every instrument is in tune and the melody never falters. Embracing this simple practice not only keeps machines happy but also boosts productivity, making the entire process a harmonious symphony of efficiency. So, let’s give our machines the care they deserve, ensuring a smooth and melodious journey in the world of Industrial Manufacturing.